Hello everyone,
I recently received one of the new 820CD charger/dischargers from the folks at TP. This is their entry into the high power charger market. Spec’s on the charger can be easily found on the net, but for F3A purposes you will be able to charge a typical 10s 5000 mAh F3A pack at approximately 4C (20A). This will provide recharge times as quickly as 15-18 minutes. Assuming of course you are able to feed it with 28V and 800W of power!
What I am going to show you in this report is how to wire up harnesses to be able to charge two (2) 10s 5000mAh Prolite V2 brick packs that have the 4mm interconnect bullets. Also how to wire two (2) Iota DLS-55 power supplies in order to give you the 28V and power required to charge these two packs in 30 minutes.

Out of the box you are presented with a very nice looking package. Slightly larger than the previous 1010C charger. You will see a larger nicely backlit LCD screen with two line display, sealed raised face buttons that are easy to push yet give a positive feel. Two fans (one for each port) force heated air out the rear of the charger. Connections for the balance boards are on each side of the charger as is the mini-USB update port. You will also notice two charge ports!

The first order of business is to get the power supplies ready for action. I have Dean’s connectors on my DLS-55’s, so it was very easy for me to wire them in series with a simple series adapter as shown in the picture. If you are not familiar with how to wire DC in series there are lots of pages on the internet to help.

When done this was how mine looked. Now the Iota power supplies have a small telephone jack to boost the voltage from a float voltage to a fast charge voltage (approximately 13.6V to 14.2V). With both of these jacks plugged in you will get a too high input voltage warning on the 820CD. Remove one and leave one in, this gives you as close to 28V as possible. If you remove both your peak current will be automatically reduced slightly by the charger to compensate for the lower input voltage.

Now lets get to work on the charger. Here is the charger with the balance boards connected. There are connections on the balance board for all TP connectors as well as 2s to 8s connectors for other popular brands.

In the box comes 4 leads for making your own charge cables. The leads already have the 4mm bullets soldered to them for connecting to the charger. In order to make the leads such that you can charge a 10s brick pack with interconnects you need to solder a 4mm socket onto one of the positive leads, a 4mm male to the negative lead, and your favoured connector to the remaining two leads as shown in the picture. This process is also described in the manual.
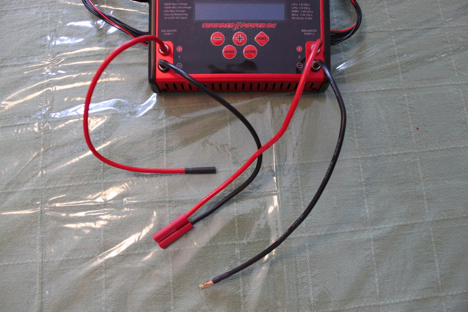
The above leads need to be connected to the charger as shown here for the correct polarity. Essentially you will be charging each 5s portion of the pack on each of the two charger ports.
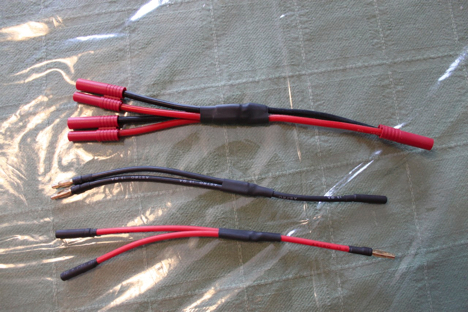
In order to charge two 10s 5000 mAh brick packs you will need to build some parallel adapters. This guide assumes you understand the principles for making parallel connections. It is pretty straightforward as you are simply branching a single to a double keeping the polarity constant. You need branches for both interconnects as well as the main leads.

You also need to build parallel adapters for the balance leads. I took 4 balance extensions and built these two parallel adapters. Same principles apply, you are simply branching a single wire to a double keeping the polarity the same. One note of caution on the balance leads. My leads were not all color coded the same, so it is important to ensure that you are wiring them truly in parallel and not simply by color, as in my case that would have resulted in a direct short across the leads.

Now we have all our leads built, we can start connecting the packs. These are the two packs I will be using, very standard packs used in F3A. These batteries were both fully discharged, one was 37.3V and the other was 37.7V. These voltages will equalize when parallel connected. A small mismatch is not a problem, but I would be cautious if your packs are more than 5% different (37.5 to 38.5V). Typically in F3A our flights are so consistent that this is not normally a problem.

Leaving the packs with the interconnects attached, the first thing I do is plug in the main lead parallel adapter. This will immediately equalize the voltage between the two. When I did this the voltage was about 37.5V.
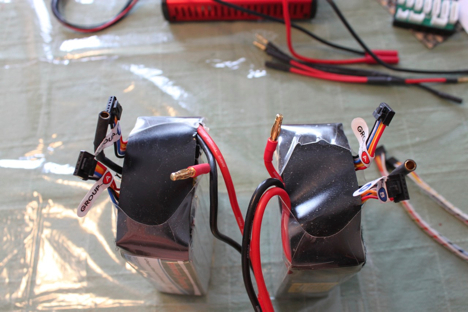
Next break apart your interconnect leads.

Now connect up both your positive interconnect parallel cable and your negative interconnect parallel cable as shown.

You can now connect your parallel adapter cables to the charger cables we made up and installed earlier. As always double and triple check all your polarities the first time to ensure that you have made all the solder connections correct. Before you start connecting batteries, go ahead and power up your charger.

Now go ahead and connect up Group A of your balance connectors to the parallel balance adapter we made, and then to the Port 1 balancer board. It is important that Group A be connected to Port 1, because the primary negative lead from the batteries are connected to Port 1. Go ahead and do the same for Group B and Port 2.

Once Group B is connected, we are ready to charge. Your final setup should look something like the picture above.
Perform the setup on both ports (port 1 shown in the picture) to charge a 5S lipo at the maximum current possible, in my case 19A was all I could set. Set the capacity (CP) to the maximum as well so that you wont shut down on capacity limit. Ensure the balance circuit is turned ON for safety reasons.

Double check all your cell voltages before the start of the charge just to be certain everything is A-OK. With the high rates of the charger things happen very quickly!

Once you are comfortable that everything is set correctly, hold down the enter key to start the charge, and repeat for the second port. The charger ramps up very fast, you can see here only 18 seconds into the charge we are already at peak current. The voltage displayed is the current battery voltage for the selected port.

There are two other screens available by pressing the +/- keys. One is the cell voltage shown here.
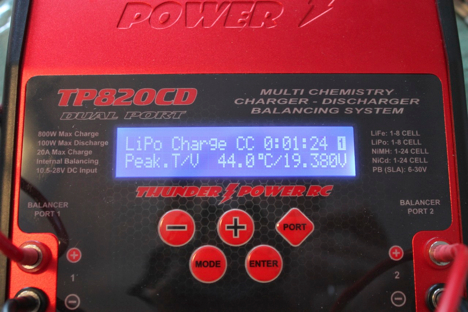
The other shows the chargers max temperature. During my charge the charger reached a peak of about 60 degrees C. The fans were at full speed for most of the charge duration.

5 minutes into the charge 1600 mAh has gone to the packs (800 each). I am expecting over 7000 mAh total.

At 10 minutes in a little over 3000 mAh has went to the packs.

15 minutes in over 4600 mAh, this is easily over halfway from a capacity standpoint. WOW!
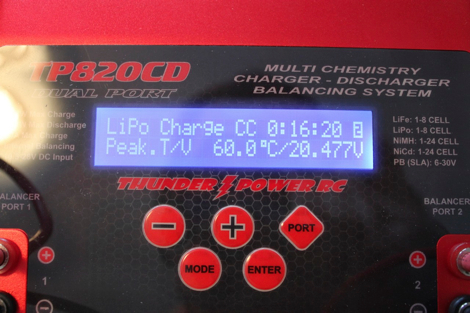
We have also reached our peak internal temperature of 60C.
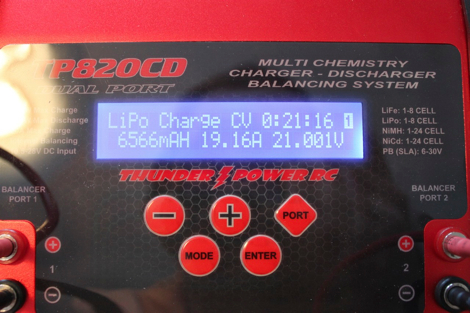
21 minutes into the charge we have put 6566 mAh into the packs, and reached peak voltage of 21V so the charger has moved to CV (constant voltage) mode.

25 minutes in the charger has ramped down to 5.5A, sent 7255 mAh into the packs and is nearing the end of the charge cycle. Remember this is for TWO (2) 10s 5000 mAh batteries!

At just under 33 minutes the charger is finished, sending 7685 mAh (~3840 mAh each) into the packs. If you had only a single pack connected to this charge you would have completed in about 16-18 minutes. I have also done this since getting the charger (4C) charge, and it will come in very handy for those times you really need another flight!
So far I have found the 820CD very simple to use. If you are familiar with the operation of the 1010C charger then you will notice many similarities between the two with respect to operation. The construction is very good, and superior to the 1010C in almost every regard.
I have not yet tried this connected to my Honda 1000i generator. However, a 10S pack being charged at 19A is 798W peak, I expect that the Honda will have a hard time handling that amount of power. The charge current may have to be reduced slightly to allow charging from a 1000W generator. This should be more than do-able for a 2000W generator though.
To download as a PDF file click below,
http://www.mediafire.com/?gkqriqabxezxq3vI hope you enjoyed the walk-through, if you have any questions drop me an email!
chad@f3acanada.orgChad